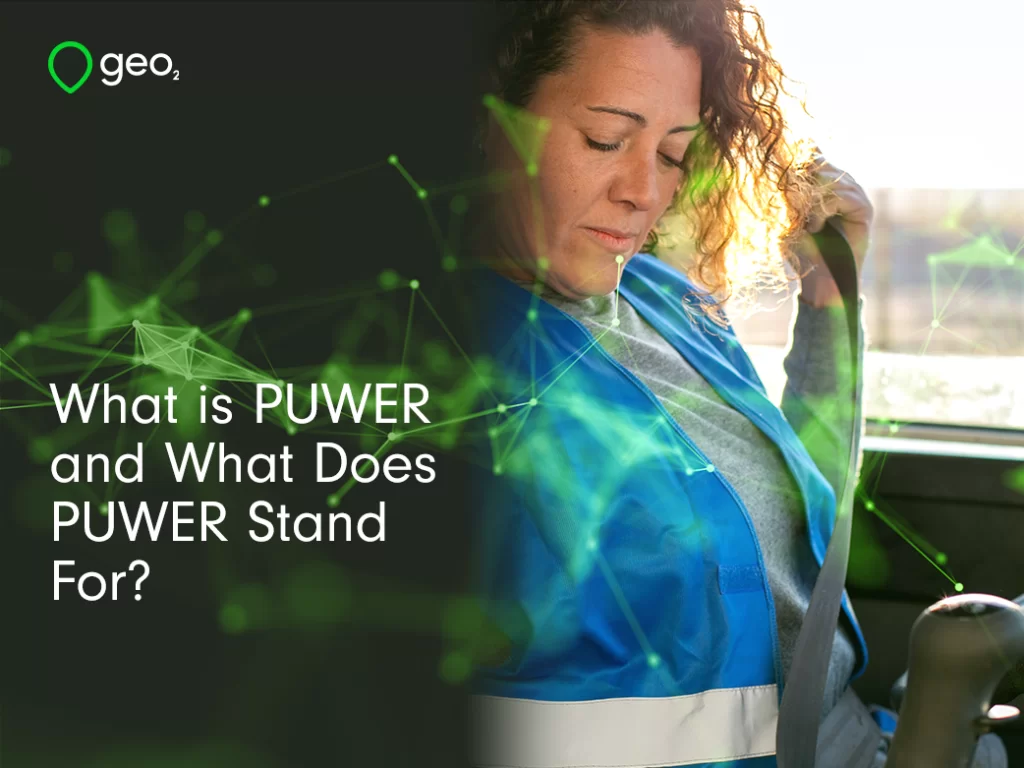
What is PUWER and What Does PUWER Stand For?
Ensuring the safety and welfare of employees within the workplace is a critical responsibility for any organization. This commitment not only protects workers but also serves to maintain productivity and uphold legal obligations. Central to this task is the understanding and implementation of key safety regulations—one of which is PUWER. But what does PUWER stand for, and why is it essential for workplace safety managers and compliance officers to ensure a safe conditions for employees?
This article explores what the regulations cover.
Need help choosing a TMS?
Download the Free Guide Now.
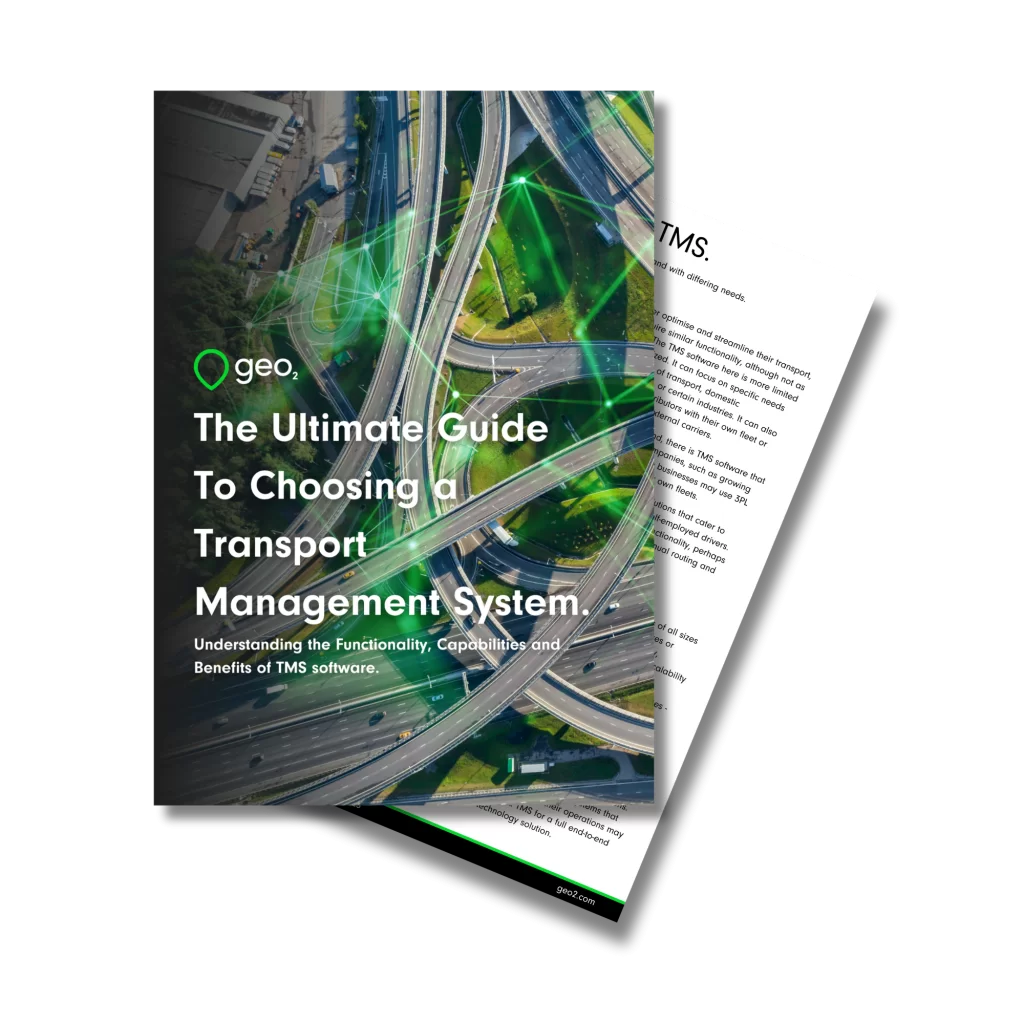
Table of Contents.
Introduction.
Countless acronyms dominate the workplace health and safety standards. PUWER stands out as a fundamental part of the safety management system. Yet, without a clear and thorough grasp of what PUWER means and its vital regulations, organizations could be at risk of leaving employees vulnerable and businesses exposed to legal repercussions.
What is PUWER?
The Provision and Use of Work Equipment Regulations, commonly abbreviated as PUWER, sets the groundwork for safety in the usage of work equipment. PUWER applies to a broad range of tools, machinery, and devices utilized in virtually every sector, placing specific responsibilities on employers and businesses.
It is an integral part of UK law, designed to ensure that all equipment provided for use at work is suitable for its intended purpose, safe for use, properly maintained, and accompanied by suitable safety measures.
Table of Contents.
Key Requirements of PUWER:
PUWER Inspection and Maintenance of Work Equipment.
One of the main provisions covered by PUWER is the regular and thorough inspection and maintenance of work equipment. Workplace safety managers must ensure that inspections are conducted by competent individuals and that any issues are addressed promptly to prevent equipment failures and potential accidents.
Training and Competence of Employees.
Ensuring employees are thoroughly trained and deemed competent in the use of work equipment is another critical aspect of PUWER. Under the Regulations, staff should receive adequate training accompanied by detailed operating instructions to mitigate user error and equipment misuse.
Risk Assessments and Control Measures.
Risk assessments under PUWER require employers to evaluate the risks associated with the use of equipment and implement the necessary control measures. This includes ensuring that any equipment is installed correctly and that protection devices such as guards, emergency stop buttons, and warning devices are in place and fully functional.
Information and Instruction for Safe Use of Equipment.
Providing clear information and instructions for the safe use of equipment is crucial. This not only includes hands-on training but also accessible guides or manuals that outline the correct use of the equipment and the risks involved.
Benefits of PUWER Compliance:
Improved Safety for Employees.
By adhering to PUWER standards, employers create a safer environment that minimizes the potential for workplace injuries due to faulty or improperly used equipment.
Reduced Risk of Accidents and Injuries.
A direct benefit of improved safety is the decrease in the likelihood and severity of work-related accidents and injuries. This can have a significant impact on the well-being of employees and the operational efficiency of a business.
Legal Compliance and Avoidance of Penalties.
Compliance with PUWER is not merely a best practice—it’s a legal requirement. Workplace safety managers must understand that PUWER compliance helps organizations avoid costly legal penalties and reputational damage.
Challenges and Common Pitfalls:
Lack of Awareness and Understanding of PUWER.
A common challenge in PUWER compliance is the lack of awareness or understanding of its scope and requirements. Workplace safety managers must regularly educate themselves and their employees on PUWER’s mandates.
Identifying and Addressing Non-Compliance Issues.
Recognizing non-compliance issues can be difficult, especially in complex work environments. Regular audits and inspections are essential for timely identification and rectification of such concerns.
Implementing Effective Risk Assessments and Control Measures.
Designing and executing effective risk assessments and control measures require a strategic approach and attention to detail. This includes regular reviews and updates to account for new risks or changes in equipment.
Conclusion
PUWER stands for more than just regulatory compliance; it is about an unwavering commitment to creating and maintaining a secure workspace. Workplace safety managers and compliance officers must take a proactive stance by keeping abreast of the nuances involved in PUWER’s regulations. By doing so, they ensure that health and safety remain paramount in their organizational ethos, protecting both their workforce and their enterprise.
Workplace safety goes beyond mere adherence to protocols—it’s a persistent culture that nurtures vigilance, preparedness, and reiterative learning. So prioritize PUWER in your safety strategies, cultivate widespread understanding within your teams, and build a foundation of security that allows every member of your organization to thrive safely and effectively.
Remember, PUWER isn’t just about fulfilling a legal duty; it’s about upholding the peace of mind that comes with knowing that everything possible is being done to protect life and limb in the workplace. Aim for excellence in safety, and let compliance follow naturally.