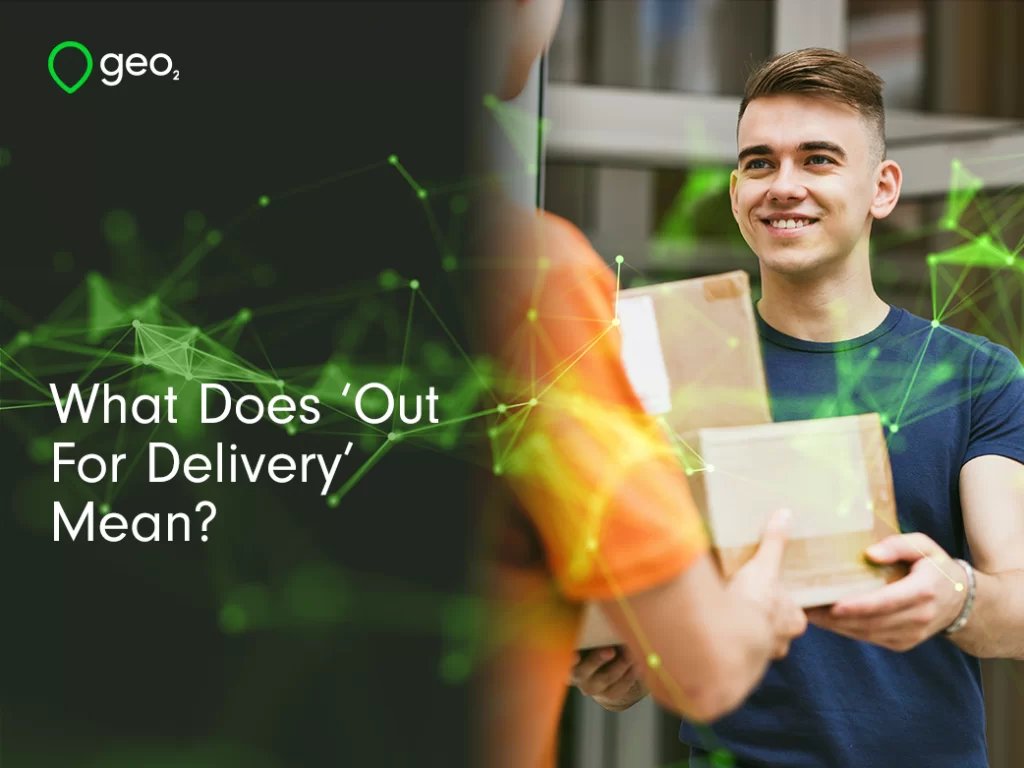
What Does ‘Out for Delivery’ Mean?
Introduction.
In logistics and distribution, the term ‘out for delivery’ can be so much more than just a status update. For the customer at least, it’s a promise that signals an imminent arrival – often the delivery of an order that is eagerly anticipated.
It marks a crucial phase in the journey of a package. For logistics companies and independent delivery drivers, understanding the nuances of this stage is essential in delivering efficient operations and customer satisfaction.
So, what exactly does ‘out for delivery’ mean and how does it fit into the delivery process as a whole?
Need help choosing a TMS?
Download the Free Guide Now.
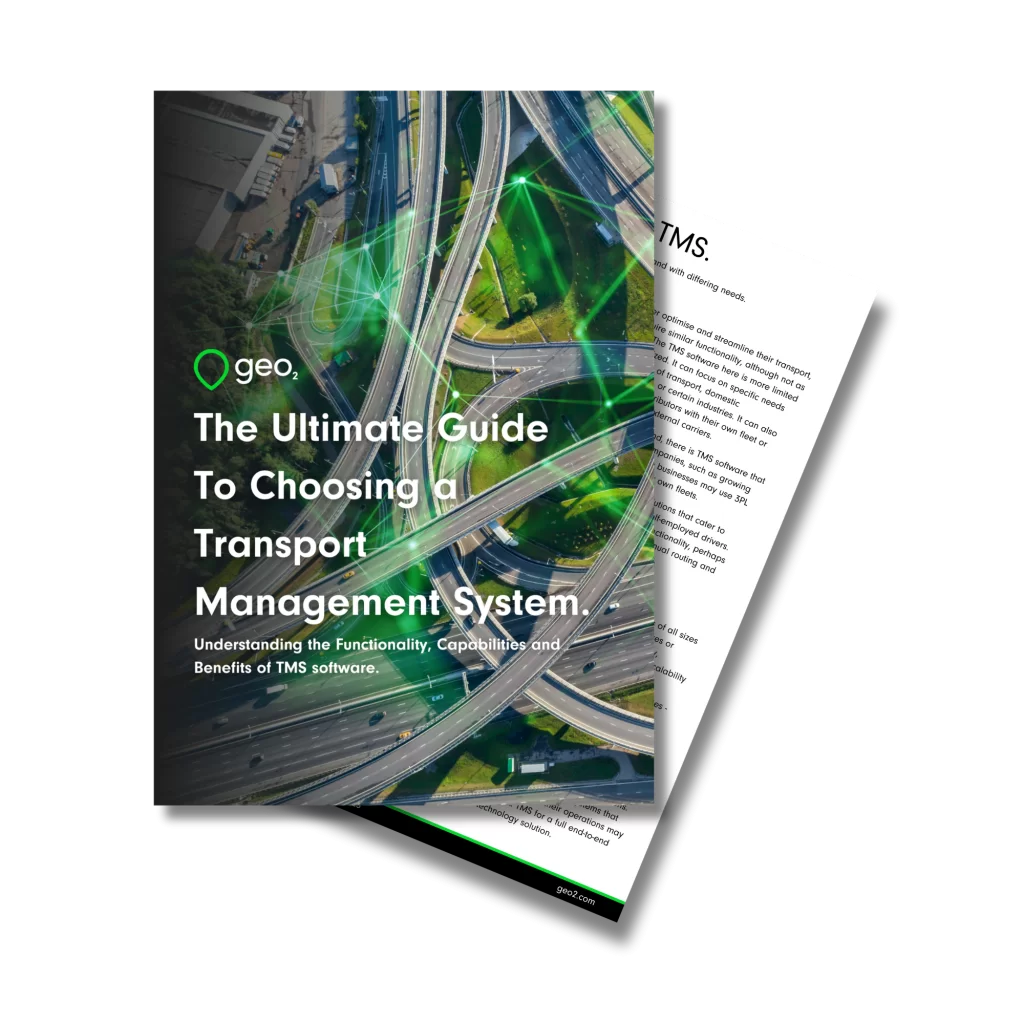
Table of Contents.
The Basics of 'Out for Delivery' Status.
Out for delivery is a term widely used in logistics to indicate that a package, parcel or shipment has left its final warehouse or depot and is now on its way to the recipient.
‘Out for delivery’ falls within last mile delivery. Unless the package is undelivered or will later be returned, ‘out for delivery’ signifies that the order is now in the final stage of the supply chain process.
In short, ‘out for delivery’ means that the package is in the final leg of its journey and is en route to the recipient or customer. Barring any issues, this also indicates that the item will be delivered that same day.
Table of Contents.
Is ‘Out for Delivery’ the Same as ‘In-Transit?’
There are other terms that are often confused with ‘out for delivery’, but which denote different stages in the overall delivery process. For example, if you see ‘in transit’, ‘manifested for delivery’ or ‘left the processing depot’, these are not the same as ‘out for delivery’.
‘In transit’ is a status that is often confused with ‘out for delivery’. The term denotes movement and that a package has left one place for another. However, it does not mean the same thing as ‘out for delivery’.
In contrast, ‘in transit’ simply means that the order has been shipped from one handling facility to another. It has not yet begun its final stage of the journey. It could, for example, be moving from a large warehouse to a regional depot. Or, it may have left the manufacturer and be en route to the distributor’s warehouse.
Equally, with long distance deliveries or those going across borders, several carriers may be involved. Each stage will be updated in the status and the package may need to move through several different stages before the final delivery stage. Until the last mile delivery, the status for the preceding stages will show as ‘in transit’.
The ‘out for delivery’ status is reserved only for packages once they are scanned and assigned to the vehicle for final delivery to the end customer.
The Impact of ‘Out for Delivery’ Status.
For ecommerce businesses, distributors and courier companies alike, the ‘out for delivery’ stage of the supply chain process plays an important role in defining the overall success of the delivery experience.
How orders are handled and delivered during the ‘out for delivery’ stage crucially shapes customer perceptions and experiences. In turn, this impacts their views of both the supplier and the delivery company. It is at this point that customer anticipation peaks and expectations are at their highest. Delays or delivery issues during this stage can significantly affect customer trust and loyalty and tarnish brand perceptions.
‘Out for delivery’ is therefore a particularly critical moment in the customer journey, where the reliability, efficiency and communication skills of the delivery service are put to the test. The overall experience directly influences the likelihood that the customer will repurchase from that supplier or recommend that particular delivery company.
Does ‘Out for Delivery’ Mean That Delivery Will be Made Today?
In the main, an ‘out for delivery’ status will signify that the delivery will be made that day. Most carrier companies will load packages for delivery first thing in the morning. Deliveries will be made up of those that were received the day before and were too late to get onto a delivery route, or those that have been received overnight.
Vehicles are filled with their scheduled deliveries for the day and they will be made during the remaining working hours. So, it is often first thing in the morning that the customer is told that their order is ‘out for delivery’.
While it can reasonably be expected that these packages will arrive on the same day that they are designated as ‘out for delivery’, any number of issues could delay delivery. For example, a broken-down delivery vehicle or particularly bad weather conditions. In another scenario, if the package has been scanned but put onto the wrong vehicle by mistake, it will have to be returned to the depot and delivery reattempted at another time.
Some of these issues are unavoidable and good delivery companies will always do their best to rectify things as soon as possible. Delivery may still be possible that day, by sending it out on another route. But weather problems for example, may mean it is likely that the package will arrive the following day.
Other mishaps or incidents can delay an ‘out for delivery’ package even further. Parcels could be stolen while out for delivery – from a vehicle or by delivery personnel – meaning that the order will need to be resubmitted. This will restart the entire order process. Some carriers or distributors will expedite a delivery like this, so as not to inconvenience the customer too much.
Ensuring the ‘Out for Delivery’ Stage Runs Smoothly.
In terms of customer satisfaction, it’s vital that delivery companies try to achieve a smooth final stage delivery process. But keeping customers happy is just one aspect of an optimal delivery operation.
Other factors that need to be considered that will ensure cost-effective and efficient operation. For example, minimising costs, maximising delivery speeds, shortening driving distances and limiting fuel consumption.
By keeping vehicles in good condition, delivery companies reduce their risk of a serious breakdown that could wipe out a route for a day – or even longer. Using walkaround vehicle checks and scheduling preventive maintenance for a fleet can ensure vehicles are always roadworthy and reliable, minimising potential disruptions to their service.
Route planning and optimisation reduces the time that drivers spend on the road. This helps them make more deliveries every day and ensures that customers receive their goods on time. It also limits fuel consumption and minimises other vehicle running costs.
Of course, there’s not much that can be done to avoid the kinds of adverse weather conditions that may prevent a successful delivery. However, delivery companies can anticipate and mitigate other on-the-road hindrances. For example, real-time dynamic routing can help drivers to avoid traffic blockages or navigate quickly around unexpected road closures. This avoids drivers sitting in traffic while the clock ticks on and their delivery schedules fall ever further behind.
By pre-empting and handling such issues, a delivery company can make sure that its ‘out for delivery’ status is not overly long and that it quickly changes to ‘delivered’.
How Customers Can Help During the ‘Out for Delivery’ Phase.
It’s not just the delivery company that can expedite a delivery. The customer too can influence how quickly and efficiently the delivery stage is achieved.
Clear delivery instructions – including alternative delivery arrangements – will always help. Then, if the customer is not in for a delivery, it can be left according to their requests, whether that’s in a safe place, with a trusted neighbour, or even returned to the delivery depot.
By keeping an eye on the status of an order and knowing when it is ‘out for delivery’, the customer can prepare for the delivery by arranging to be in or diverting the package. If a signature is required, for example, the customer being out will mean it either has to be redelivered, or the delivery driver has to find an alternative delivery location with a suitable signatory. Either of these will delay the delivery of the package.
Technology and 'Out for Delivery'.
With the advent of sophisticated tracking systems and digital tools, transport managers and customers alike are able to closely monitor orders during the ‘out for delivery’ stage.
Modern logistics operators rely heavily on technology to update the ‘out for delivery’ status. This is typically achieved through a combination of GPS tracking, mobile technology and transport management software.
When a package is loaded onto a delivery vehicle, its status is updated to ‘out for delivery’ in the tracking system. This is often done automatically, triggered by the package barcode being scanned, which accurately records and communicates the order’s progress.
Transport management systems (TMS) that employ GPS technology enable tracking of the delivery vehicle in real time. This helps the delivery company to give the customer a precise delivery window.
Real-time tracking technology enhances route optimisation, allowing for quicker and more efficient delivery routes, saving time and reducing costs. It also aids in managing customer expectations and improving delivery accuracy. In the case of any delays or unexpected issues, delivery companies can proactively manage the situation by providing updates for customers.
From a customer’s perspective, real-time tracking offers a sense of control and reassurance. Knowing exactly when their package is ‘out for delivery’ and being able to track its progress each help to significantly improve the delivery experience. This level of transparency also helps improve satisfaction, as customers are not left guessing the whereabouts of their delivery and can also plan their day around it.
TMS technology also facilitates better communication between delivery companies and customers once the ‘out for delivery’ status begins. If the customer will not be available to receive their package, alternative arrangements can be made, which reduces the likelihood of failed deliveries.
Geo2 provides a range of features for delivery companies and individual drivers. It offers dynamic live tracking of vehicles and orders, featuring comprehensive status updates that you can also make accessible to your customers. Discover how supplying ‘out for delivery’ information could improve your delivery operations, book a free consultation or try for free today.